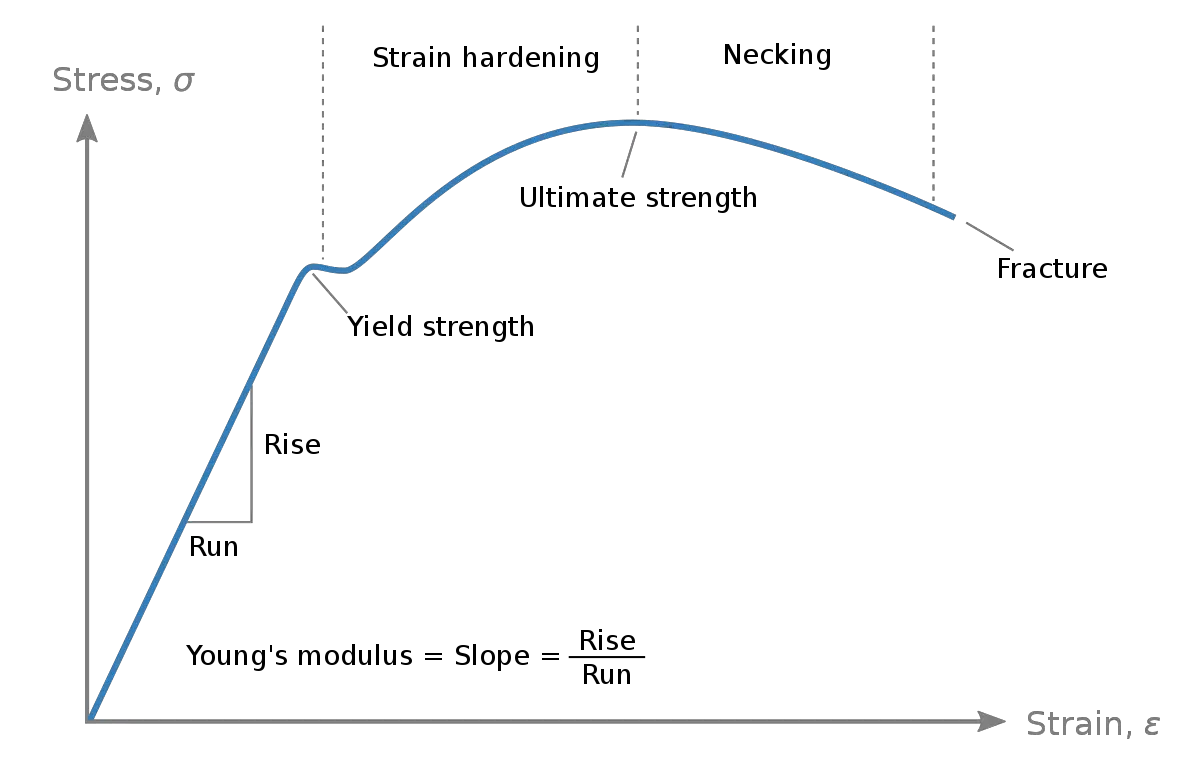
Introduction: Within the realm of materials science and engineering, delving into the mechanical behavior of metals is paramount. Central to this exploration is the stress-strain curve, a foundational concept that sheds light on how materials respond to external forces. This article delves into the intricacies of the stress-strain curve, elucidating its significance, components, and real-world applications.
Defining the Stress-Strain Curve: The stress-strain curve is a graphical representation of the relationship between stress and strain experienced by a material under external loading. Stress, symbolized by σ (sigma), measures a material’s internal resistance to deformation, while strain, denoted by ε (epsilon), quantifies the material’s deformation relative to its original dimensions. By plotting stress against strain, researchers and engineers gain crucial insights into a material’s mechanical properties, including stiffness, strength, ductility, and toughness.
Key Components of the Curve:
-
- Elastic Region (Proportional Limit): In the initial stage of loading, the stress-strain curve displays a linear relationship within the elastic region. Here, the material behaves elastically, meaning it returns to its original shape once the applied load is removed. This linear behavior adheres to Hooke’s Law, where stress is directly proportional to strain. The slope of this linear portion, known as the elastic modulus or Young’s modulus (E), quantifies the material’s stiffness.
-
- Yield Point: Beyond the elastic limit lies the yield point, marking the onset of plastic deformation. At this juncture, the material begins to deform plastically under increasing stress. The yield strength (σ_y) represents the stress at which this transition occurs, indicating the maximum stress a material can withstand without experiencing permanent deformation.
-
- Plastic Region: Post the yield point, the stress-strain curve enters the plastic region, characterized by non-linear deformation. In this phase, the material undergoes irreversible changes in shape with increasing strain. Mechanisms such as dislocation movement and grain boundary sliding dominate the material’s response to stress. The ultimate tensile strength (UTS) signifies the maximum stress reached before fracture occurs.
-
- Necking and Fracture: Ductile materials experience localized necking beyond the UTS, where the cross-sectional area significantly decreases. Ultimately, fracture occurs at the point of minimum cross-section, marking the specimen’s failure. In contrast, brittle materials often fail abruptly without notable necking.
Real-World Applications:
-
- Material Selection: Engineers employ stress-strain curves to assess and compare the mechanical properties of various materials, aiding in the selection of suitable candidates for specific applications. For instance, applications requiring high strength and stiffness may prioritize materials with elevated yield strength and elastic modulus.
-
- Structural Design: Understanding the stress-strain behavior of metals is crucial in designing structures and components to withstand anticipated loads and environmental conditions. By conducting stress analyses considering factors such as load distribution, material properties, and safety margins, engineers ensure structural integrity and reliability.
-
- Quality Control: In manufacturing processes, monitoring the stress-strain behavior of metals facilitates quality control and assurance. Tensile tests on representative samples enable manufacturers to verify material properties, detect defects, and ensure compliance with specifications and standards.
-
- Failure Analysis: Analyzing stress-strain curves of failed components offers valuable insights into failure mechanisms and root causes. This information aids engineers in refining design practices, implementing preventive measures, and mitigating the risk of future failures.
Conclusion: The stress-strain curve serves as a fundamental tool in deciphering the mechanical behavior of metals, offering profound insights into their elastic, plastic, and failure characteristics. Through comprehensive analysis, researchers and engineers make informed decisions regarding material selection, structural design, quality control, and failure analysis, advancing the fields of materials science and engineering. As exploration continues, the stress-strain curve remains a cornerstone in our quest for innovation and excellence.